5 Types of Galvanizing Methods You Should Know About
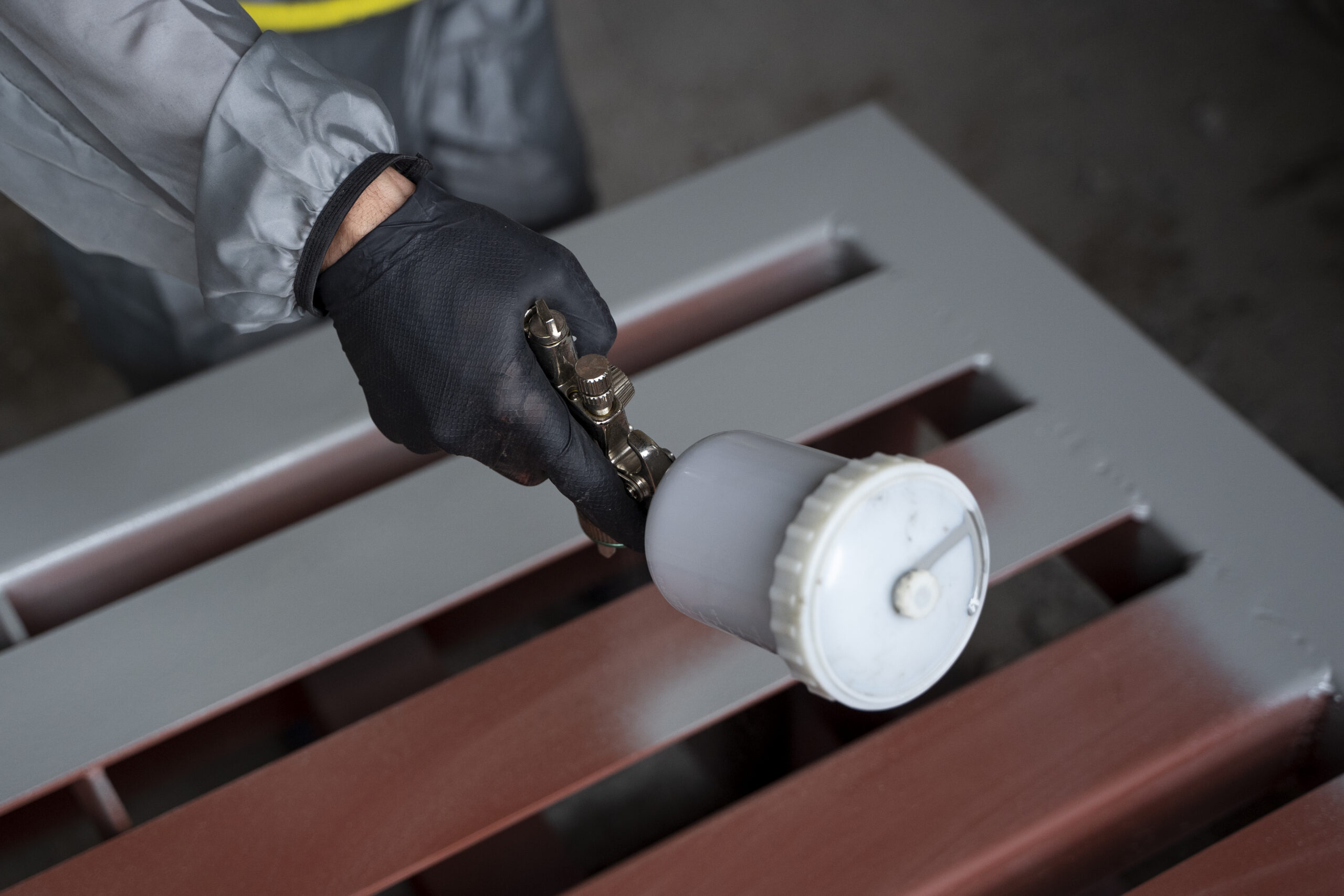
Galvanizing is a vital system in cutting-edge industries, imparting prolonged-lasting protection to metals in competition to corrosion. Applying a zinc coating to metallic or iron, it acts as a guard, preventing rust, and is placed on because of publicity to the surroundings. This technique is vital in sectors like creation, car manufacturing, and agriculture, wherein metallic additives are exposed to moisture, air, and other corrosive factors.
Different techniques have been evolved to cater to particular industrial desires. Each approach offers particular benefits in phrases of durability, end, and price-effectiveness.
Hot-Dip Galvanizing
Hot-dip galvanizing is one of the most commonly used methods for protecting metals from corrosion. This technique includes immersing a steel item right into a bathtub of molten zinc heated to about 450°C. The molten zinc reacts with the ground of the steel, developing a chain of zinc-iron alloy layers and a top layer of natural zinc.
The device begins with a thorough cleansing to eliminate all dirt, grease, and rust from the floor. Once easy, the item is dipped into the molten zinc bathtub. After being removed, it cools, and the zinc coating hardens to shape a durable barrier.
Hot-dip galvanizing is especially relevant for huge, exposed systems together with bridges, light poles, and application pipelines. Its thick, robust coating offers super protection in opposition to climate conditions and pollutants, making it ideal to be used in industrial zones and coastal areas. The durability of this method guarantees that the coating can very last for numerous a long time with minimum upkeep, imparting considerable lengthy-term charge financial savings.
Additionally, warm-dip galvanizing gives whole coverage, along with difficult-to-reap corners and crevices. This ensures that every part of the shape is nicely protected, even within the most difficult environments.
Electro galvanizing
Electro galvanizing is a noticeably managed technique that makes use of an electric-powered current to deposit a layer of zinc onto the floor of the metallic. Unlike hot-dip galvanizing, which immerses the metallic in molten zinc, happens in an electrolytic bath containing zinc ions. The electric-powered modern causes the zinc to paste to the floor, forming a clean, even coating.
This approach is commonly applied in industries in which aesthetics and precision are critical. For example, the automobile agency frequently makes use of electro-galvanized steel for car body panels, providing moderate corrosion protection and an elegant quit. Additionally, it is utilized in manufacturing home domestic devices, digital components, and ornamental furnishings.
The primary benefit of electro-galvanizing lies in its capability to govern the thickness of the zinc coating exactly. This is vital for packages requiring nice tolerances or wherein weight is a topic. However, due to the truth, that the coating is thinner than that of hot-dip galvanizer, it could no longer provide an equal degree of corrosion resistance.
Despite this impediment, electrogalvanizer remains a preferred preference for products that need a graceful look, because it produces a smoother quit without the rough texture sometimes associated with different techniques.
Sherardizing
Sherardizing, additionally called vapor galvanizing, is a totally precise technique that consists of heating the steel and zinc powder in a sealed, rotating drum. The method is conducted at temperatures between 320°C and 500°C. As the zinc powder vaporizes, it bonds with the metal floor to create a long-lasting zinc-iron alloy coating.
This approach is ideal for small and complex additives which include nuts, bolts, screws, and gears. These gadgets often have complicated shapes or threads which can be tough to coat lightly with the use of different techniques. Sherardizing guarantees a uniform coating, even in tough-to-gain regions.
One of the critical aspects advantages of sherardizing is its resistance to hydrogen embrittlement—a phenomenon wherein metals emerge as brittle due to hydrogen absorption during certain strategies. This makes sherardizing a favored desire for high-energy metallic additives that require every sturdiness and structural integrity.
The corrosion resistance offered through sherardizing is fantastic, making it suitable to be used in annoying environments. Industries along with the introduction, of automobiles, and heavy machinery rely upon this approach to enhance the overall performance and lifespan of their components.
Continuous Galvanizing
Continuous galvanizing is an excessive-pace, computerized device designed for the massive-scale manufacturing of metal sheets, strips, and wires. In this technique, the metal is exceeded through a molten zinc tub on a continuous production line. After being protected, the fabric is swiftly cooled and dealt with to form a uniform layer of zinc.
This method is particularly green for producing roofing sheets, fencing substances, and corrugated metallic merchandise. It is also typically used for growing metal ducts, pipes, and electrical conduits. The velocity and efficiency of continuous galvanizing make it perfect for manufacturers needing to deliver massive portions of fabric in a short time.
Continuous galvanizing guarantees a regular coating thickness, which is important for maintaining quality at some point in all merchandise. The technique is likewise extraordinarily price-powerful, as it minimizes waste and allows for seamless integration into existing production strains.
While the zinc coating in continuous galvanizing is thinner in the evaluation of distinct strategies, it offers dependable corrosion resistance. This approach is often selected for programs in which the metallic isn’t always subjected to immoderate environmental conditions but calls for adequate safety.
Mechanical Galvanizing
Mechanical galvanizing, or peen plating, is a chilly method wherein zinc powder is mechanically bonded to the metal surface. This is accomplished by placing the metallic elements in a rotating drum with zinc powder and tumbling media. As the drum rotates, the zinc debris is hammered onto the ground, creating a uniform and sturdy coating.
This technique is specifically effective for small objects together with screws, washers, nails, and other fasteners. Unlike heat-dip galvanizing, mechanical does not contain high temperatures, which reduces the hazard of changing the metallic’s mechanical homes. This is specifically crucial for additives that require precise dimensions or flexibility.
Mechanical galvanizing is likewise environmentally fine because it avoids using chemical compounds or excessive power strategies. It is broadly utilized in construction and production industries, in which corrosion resistance is vital for smaller elements uncovered to the factors.