3D Printing vs Traditional Manufacturing: A Comprehensive Comparison
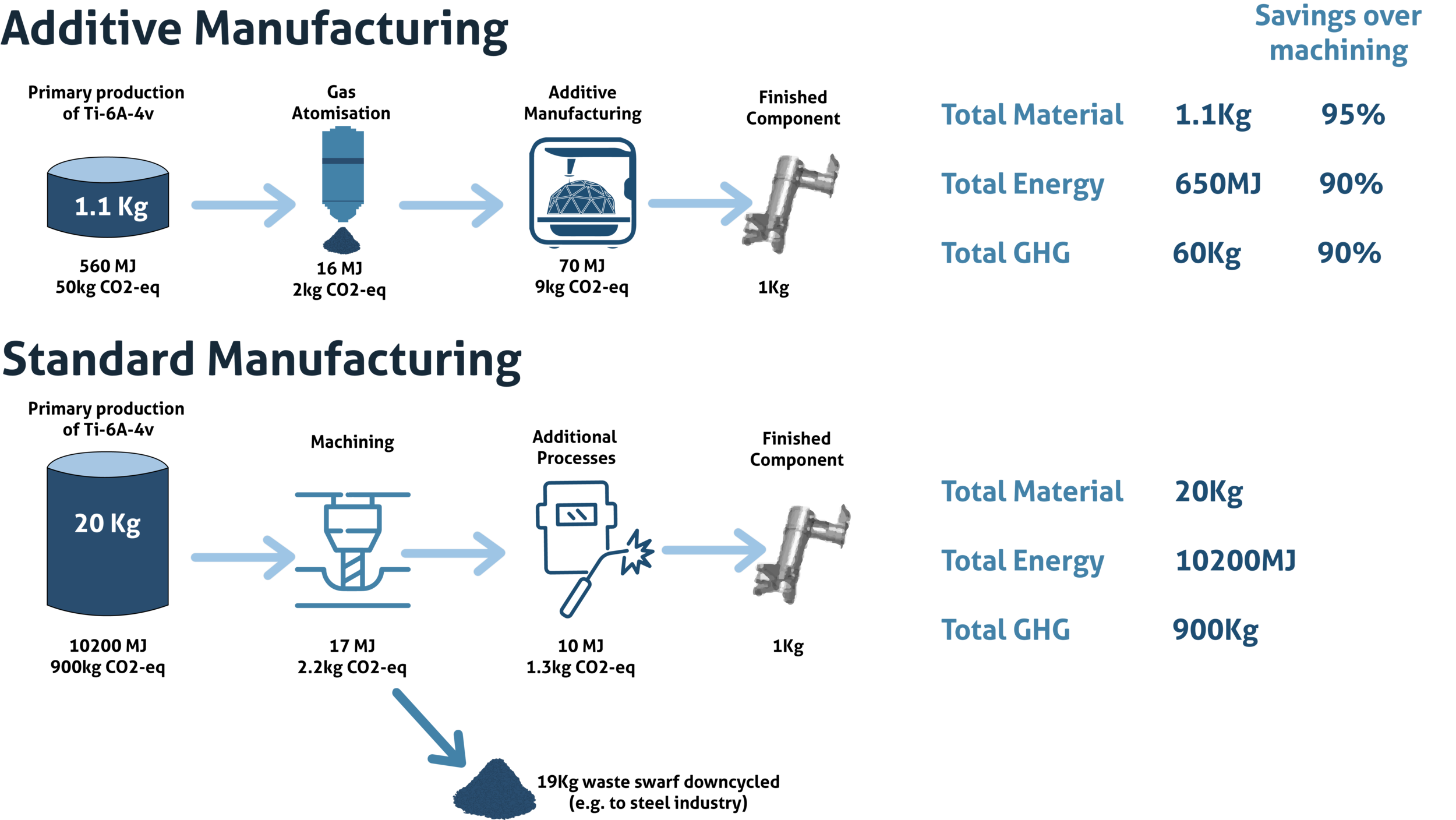
In recent years, the manufacturing industry has been witnessing a remarkable transformation driven by new technologies. Among the most groundbreaking developments is 3D printing, which has emerged as a revolutionary method of producing goods. In contrast, 3D Printing vs Traditional Manufacturing, such as injection molding, machining, and casting, have been the backbone of industrial production for many decades. This article will compare 3D printing with traditional manufacturing methods, discussing their respective strengths, weaknesses, and applications to understand which is better suited to different industrial needs.
Introduction to 3D Printing and Traditional Manufacturing
What is 3D Printing?
3D printing, also referred to as additive manufacturing, is a process of creating three-dimensional objects by adding material layer by layer based on a digital design. This approach contrasts with traditional manufacturing, which typically involves shaping or cutting material to create the desired object. Materials used in 3D printing include a variety of plastics, metals, resins, and even concrete, and it is often used for prototyping, creating small production runs, and producing complex geometries.
What is Traditional Manufacturing?
Traditional manufacturing encompasses a wide range of processes such as machining, injection molding, casting, stamping, and die casting. In these methods, raw materials are manipulated using cutting, pressing, heating, or molding to create finished products. Traditional manufacturing is known for its long-standing role in high-volume, mass production and is typically used when high precision, cost-effectiveness, and efficiency are essential for producing standardized products.
Key Differences Between 3D Printing and Traditional Manufacturing
1. Production Process: Additive vs. Subtractive
- 3D Printing: In 3D printing, the process is additive—the material is built up layer by layer according to a digital model. This method allows for the creation of intricate shapes and structures without the need for complex tooling or molds. It is highly suitable for making prototypes or parts with complex internal geometries or organic shapes.
- Traditional Manufacturing: Most traditional manufacturing processes are subtractive (e.g., CNC machining), where material is removed from a larger block or sheet to create the final product. In processes like injection molding or die casting, material is formed by pouring or injecting it into molds. These processes are highly effective for creating large quantities of standardized parts but can be less efficient when dealing with highly complex or customized designs.
2. Material Efficiency
- 3D Printing: One of the key advantages of 3D printing is its material efficiency. Since material is added only where it is needed, waste is minimal. This is particularly advantageous when working with expensive materials or when producing small batches of custom parts.
- Traditional Manufacturing: Traditional methods can generate substantial waste, especially in subtractive processes like machining, where a significant portion of the material is cut away and discarded. In casting or injection molding, waste can occur when excess material is removed, and molds have to be replaced periodically.
3. Design Flexibility
- 3D Printing: 3D printing excels in its ability to produce complex and intricate designs that would be challenging or impossible to achieve with traditional methods. Complex internal geometries, lattice structures, and highly detailed shapes can be created without needing complex tooling or molds.
- Traditional Manufacturing: Traditional manufacturing can create relatively complex parts, but it often requires additional time and costs for tooling, especially when dealing with intricate or customized designs. For example, machining a part with an internal cavity or undercut may require additional setups or specialized tooling, which adds complexity and cost.
4. Speed and Lead Time
- 3D Printing: One of the major advantages of 3D printing is the rapid turnaround time. For prototypes or short-run production, 3D printers can produce parts quickly—sometimes within a few hours or days. This speed makes 3D printing ideal for rapid prototyping, design iteration, and small batch production.
- Traditional Manufacturing: Traditional manufacturing methods often require a longer lead time, especially when creating new molds or tooling. The setup time for injection molding or machining can be days or even weeks, depending on the complexity of the part. However, once tooling is set up, high-volume production can proceed much faster.
5. Cost Efficiency
- 3D Printing: For low-volume production, prototyping, and custom parts, 3D printing can be more cost-effective than traditional manufacturing. The lack of tooling costs, molds, and other setup expenses means that the cost per part remains consistent regardless of how many parts are produced. However, as production volumes increase, the cost per part can rise, making traditional methods more economical for large-scale manufacturing.
- Traditional Manufacturing: Traditional methods are more cost-effective for mass production of standardized parts. Once tooling is set up, the cost per unit decreases significantly as production volume increases. However, the high upfront costs for tooling and molds can make traditional manufacturing expensive for low-volume or custom production runs.
6. Customization and Personalization
- 3D Printing: Customization is one of the strongest points of 3D printing. Every part produced can be unique, allowing for bespoke designs, personalization, and flexibility. For industries where product customization is essential—such as medical devices, fashion, or small batch production—3D printing offers unparalleled advantages.
- Traditional Manufacturing: Customizing products through traditional manufacturing can be costly and time-consuming, as changes often require modifying molds or tooling. While some traditional methods, like CNC machining, offer some flexibility, they are generally less cost-effective for customization compared to 3D printing.
7. Production Volume
- 3D Printing: 3D printing is generally better suited for low-volume production, rapid prototyping, and short-run manufacturing. As the number of parts increases, the time and cost to print each part can become less efficient compared to traditional manufacturing.
- Traditional Manufacturing: For high-volume production, traditional methods are more efficient. Processes like injection molding, stamping, and die casting can produce large quantities of identical parts at a very low cost per unit. These methods are ideal for industries where large-scale production is necessary, such as automotive, electronics, and consumer goods.
Applications: Where Each Method Shines
1. Applications of 3D Printing
- Prototyping: 3D printing is widely used for creating prototypes quickly and cost-effectively. Designers and engineers can iterate and refine their designs faster by creating physical prototypes in-house rather than waiting for traditional methods.
- Medical Industry: 3D printing is particularly valuable in the medical field, where customized implants, prosthetics, and anatomical models are needed. The ability to produce patient-specific items or small batches of medical devices is a key advantage of 3D printing.
- Aerospace and Automotive: These industries benefit from 3D printing’s ability to create lightweight, complex parts. For example, parts with internal lattice structures that reduce weight without sacrificing strength can be manufactured quickly and efficiently.
2. Applications of Traditional Manufacturing
- Mass Production: Traditional manufacturing processes excel in high-volume production. Industries like automotive, consumer electronics, and appliances rely on traditional methods to produce millions of identical parts at low cost.
- Heavy Industry: For heavy industries like construction, defense, and aerospace, traditional methods such as casting and machining are better suited for producing large, durable components that can withstand extreme conditions.
- Tooling and Dies: Traditional manufacturing is also essential for the production of the molds, dies, and tooling required for various industrial processes, including injection molding, stamping, and casting.
The Future of Manufacturing: A Hybrid Approach
As both 3D printing and traditional manufacturing technologies continue to evolve, the future of manufacturing will likely see a hybrid approach, where both methods complement each other. 3D printing’s flexibility and speed will be paired with the efficiency and cost-effectiveness of traditional mass production methods. Industries that need high volumes of standardized parts will continue to rely on traditional manufacturing, while those requiring customization, rapid prototyping, or small batches will benefit from 3D printing.
In conclusion, both 3D printing and traditional manufacturing have their strengths and are suited to different applications. Understanding the differences between these two methods is crucial for businesses looking to optimize their production processes. The choice between 3D printing and traditional manufacturing largely depends on factors such as production volume, design complexity, cost, and customization needs.