Maintenance Best Practices for Turn Head Distributors in Food Manufacturing
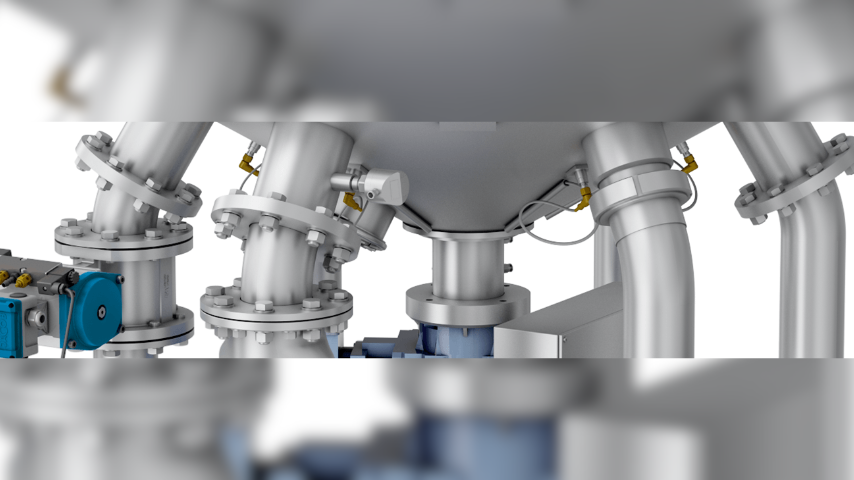
Turn head distributors are an indispensable component of any food manufacturing plant. They effectively distribute bulk materials, such as grain, powder and other ingredients, across several lines simultaneously. This keeps processes operating at their peak. Maintenance is an important activity that helps prevent sudden breakdowns, prolongs equipment life and ensures compliance to food safety regulations. In this article, we will take a look at how to maintain and service these devices, with special consideration for double turn head distributors and dust-tight versions.
Understanding the importance of regular maintenance
Turn head distributors play an important role in manufacturing plants. However, like all mechanical systems, they wear down with time. Proper maintenance will ensure that they continue to perform with the required level of accuracy and reliability, distributing materials without delays or contamination.
Poor maintenance, when precision and hygiene are essential, can lead to inefficiency or production of poor quality products, or even food safety violations. Periodic maintenance reduces these risks by keeping machines in optimal condition and identifying problems before they occur.
Key maintenance practices
Regular inspections and monitoring
Regular inspection is key in any maintenance programme. The distributor should be routinely inspected for wear and tear, misalignment and other types of damage. This will involve observing key components, including the rotating head, seals, bearings and outlet ports. Any abnormalities, such as strange noises or vibrations, should be attended to immediately.
Sensors or automated systems monitoring will also detect conditions such as changes in material flow rate or pressure imbalance. Problems can be detected early, greatly reducing the possibility for unplanned losses in operation time.
Lubrication of moving parts
Turn Head Distributors have rotating mechanisms which need periodic lubrication. Proper greasing of bearings, gears and other moving parts minimises friction, lessens excessive wear and assures even operation. However, this should be done with food-grade lubricants to preclude contamination of the product stream.
Cleaning and sanitation
In food processing, sanitisation is everything. Distributors and any galvanised steel pipe need to be cleaned on a regular basis, removing all kinds of potential residue for bacterial growth. Strict cleaning between batches with regard to allergen-controlled environments helps prevent cross-contamination. Adhering to sanitation protocols facilitates this process and ensures that regulations are met.
Special consideration for double turn head distributors
These machines are typically used in more involved operations, where several material streams are in process simultaneously. The maintenance requirements for these distributors are similar to standard versions, but with added complexity due to the dual rotating heads. They depend on precise synchronisation in which both heads are set properly in balance so that proper distribution into various lines is achieved. For this reason, the mechanism should be regularly checked to avoid misalignment and cross-contamination between product streams. Immediately correct any lag or error in the rotation of one head relative to the other.
More vigilance over wear
Of course, with two turning heads in play, there is increased wear on moving parts. Bearings, gears, and seals will have to be watched more closely than usual for signs of overuse. Due to the additional burden on the distributor, maintenance schedules may need to be shortened to avoid sudden breakdowns.
Complex cleaning procedures
These machines have more faces and inner parts that need to be cleaned. For the manufacturing of allergen-free or highly sensitive products, cleanliness is a high priority. This degree of cleaning, often requiring the disassembly of both heads, helps to ensure all parts are properly sanitised for the next production run.
Dust-tight turn head distributors: maintenance for hygiene and safety
These distributors are used where either powders or fine particles are being handled. Their dust-tight seals and gaskets avoid work area and product contamination, but these systems demand careful maintenance if they are to be kept performing effectively.
Seal integrity
Keeping it dust-tight starts with the integrity of the seals. High-quality gaskets and food grade o rings are relied on to block the escape of fine particles into the environment. They should be regularly inspected and replaced to maintain performance.
Dust buildup prevention
Even with seals, some dust may still accumulate around the distributor. It is important, therefore, that the external surfaces and the area surrounding the distributor are cleaned regularly to avoid the accumulation of dust in the facility, or in moving parts that may cause mechanical malfunction.
Monitoring for air leaks
Monitoring for air leaks, especially around seals or inlet/outlet ports, will help identify any breach in a system. Even slight leaks can result in the overall contamination of a product or loss of it; therefore, it is important that once such a leak has been identified, immediate action be taken.
Extend equipment life through proactive maintenance
A well-planned maintenance programme makes sure food production lines operate efficiently and safely, helping to reduce instances of machine downtime and associated maintenance costs.
Turn head distributors need proactive maintenance, so these critical pieces of equipment continue reliably doing their jobs, protecting product quality and safety in food manufacturing environments.